Make Your Factory More Efficient and Productive with IoT
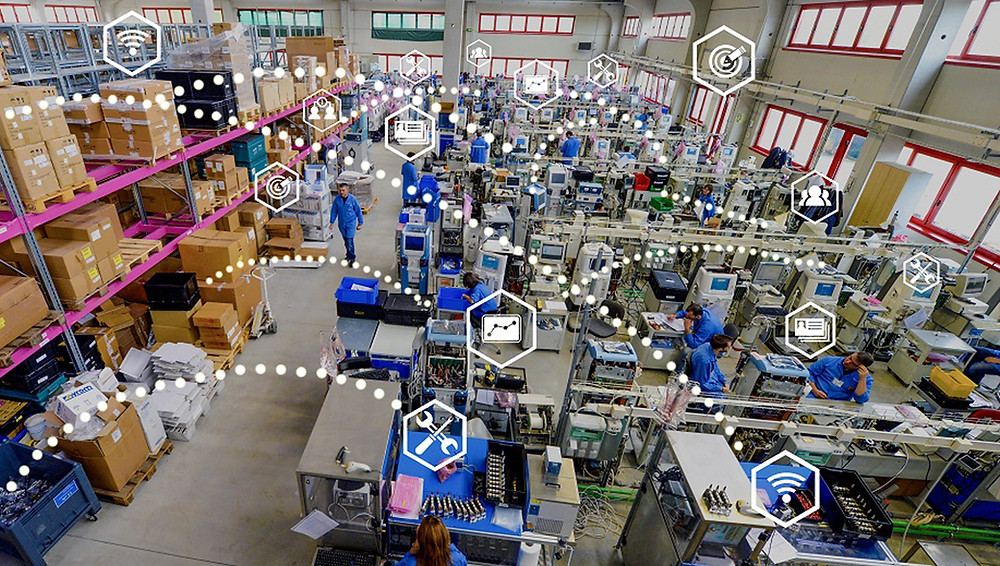
Welcome to the digital age, where cutting-edge technology is transforming the way we do business. In today’s competitive market, factories need to be more efficient and productive than ever before. That’s where the Internet of Things (IoT) comes in. By harnessing the power of IoT, factory owners can revolutionize their operations and maximize their output.
With IoT, everyday objects and machines are connected, communicating, and sharing data. This connectivity allows for real-time monitoring and control, enabling factory owners to make informed decisions and streamline processes. By integrating IoT into your factory, you can track equipment performance, manage energy consumption, and optimize production schedules.
In this article we discuss the key points to consider:
- The benefits of implementing IoT in factories
- Key components of an IoT system in manufacturing
- How to choose the right IoT solution for your factory
- Steps to implement IoT in your factory
- Overcoming challenges in implementing IoT in manufacturing
- Best practices for optimizing factory efficiency and productivity with IoT
- Real-time monitoring and predictive maintenance with IoT
- Case studies of successful IoT implementation in factories
The benefits of implementing IoT in factories
Implementing IoT in factories offers a wide range of benefits that directly contribute to increased efficiency and productivity. One of the most significant advantages is improved operational visibility. With IoT-enabled sensors and devices, factory owners can monitor every aspect of their operations in real-time. This means you can track the performance of your machines, identify bottlenecks, and make data-driven decisions to optimize your production processes.
IoT also enables predictive maintenance, which is a game-changer for factory owners. By equipping machines with sensors, you can monitor their condition and detect potential failures before they occur. This allows you to schedule maintenance activities proactively, minimizing downtime and maximizing productivity. With IoT, you can say goodbye to costly breakdowns and unexpected equipment failures.
Another benefit of implementing IoT in factories is enhanced inventory management. By tracking your inventory in real-time, you can optimize stock levels, reduce waste, and ensure that you always have the right amount of materials on hand. This not only improves efficiency but also saves costs in the long run.
Key components of an IoT system in manufacturing
To implement IoT in your factory, it’s essential to understand the key components of an IoT system. These components work together to collect and analyze data, enabling you to make informed decisions and optimize your operations.
- Sensors and devices: These are the building blocks of an IoT system. Sensors collect data from various sources, such as machines, equipment, and environmental conditions. Devices enable connectivity and communication between sensors and the central IoT platform.
- Connectivity: IoT relies on a robust and secure network infrastructure to transmit data between sensors, devices, and the central platform. Whether it’s Wi-Fi, Ethernet, or cellular connectivity, choosing the right option is crucial for seamless data transfer.
- Data storage and processing: The vast amount of data collected by IoT sensors needs to be stored and processed efficiently. Cloud-based solutions offer scalability and flexibility, allowing you to store and analyze data in real time.
- Analytics and insights: IoT data is valuable only when it can be transformed into actionable insights. Analytics tools help you make sense of the data, identify patterns, and derive meaningful conclusions that can drive operational improvements.
How to choose the right IoT solution for your factory
Choosing the right IoT solution for your factory can be a daunting task, given the wide range of options available in the market. Here are some key factors to consider when selecting an IoT solution:
- Scalability: Ensure that the IoT solution can scale as your factory grows. It should be able to handle an increasing number of sensors and devices without compromising performance.
- Compatibility: Check if the IoT solution is compatible with your existing infrastructure and equipment. Compatibility issues can lead to integration challenges and hinder the smooth implementation of IoT in your factory.
- Security: Security is a crucial aspect of IoT implementation. Make sure that the IoT solution has robust security features to protect your data and prevent unauthorized access.
- Ease of use: Look for an IoT solution that is user-friendly and easy to implement. The solution should provide intuitive interfaces and tools that allow you to monitor and manage your IoT devices effectively.
By considering these factors, you can select an IoT solution that aligns with your factory’s specific requirements and objectives.
Steps to implement IoT in your factory
Implementing IoT in your factory requires careful planning and execution. Here are the key steps involved in the implementation process:
- Define objectives: Clearly define your objectives and identify the areas in your factory where IoT can make a significant impact. This will help you prioritize your efforts and focus on the areas that will yield the most significant results.
- Evaluate andselect IoT solutions: Research and evaluate different IoT solutions available in the market. Consider the factors mentioned earlier and choose a solution that meets your factory’s requirements.
- Prepare your infrastructure: Ensure that your factory’s infrastructure, including network connectivity and power supply, is ready to support IoT implementation. If necessary, make the necessary upgrades or modifications to create a robust IoT environment.
- Install and configure sensors: Install IoT sensors in strategic locations within your factory. Configure the sensors to collect the necessary data and transmit it to the central IoT platform.
- Connect and integrate: Connect the sensors and devices to the central IoT platform. Ensure that the data is being transmitted correctly and that the devices are communicating seamlessly.
- Monitor and analyze: Once the IoT system is up and running, monitor the data collected by the sensors in real-time. Use analytics tools to analyze the data and gain insights that can drive operational improvements.
- Optimize and refine: Continuously optimize your IoT system based on the insights gained from data analysis. Fine-tune your processes, make adjustments, and implement improvements to maximize the efficiency and productivity of your factory.
By following these steps, you can successfully implement IoT in your factory and unlock its full potential.
Overcoming challenges in implementing IoT in manufacturing
Implementing IoT in manufacturing comes with its own set of challenges. It’s essential to be aware of these challenges and have strategies in place to overcome them.
- Data security and privacy: With the increasing connectivity of devices, data security and privacy become critical concerns. Implement robust security measures, such as encryption and access controls, to protect your data from unauthorized access.
- Legacy systems integration: Integrating IoT with existing legacy systems can be complex. Ensure that your IoT solution is compatible with your legacy systems and plan for the integration process carefully.
- Technical expertise: Implementing IoT requires technical expertise. If you don’t have the necessary in-house skills, consider partnering with an IoT service provider or hiring qualified professionals to assist you.
- Cost considerations: Implementing IoT can be a significant investment. Consider the upfront costs, ongoing maintenance, and potential ROI when evaluating the feasibility of IoT implementation for your factory.
By addressing these challenges proactively and having a well-thought-out implementation plan, you can minimize disruptions and maximize the benefits of IoT in your manufacturing operations.
Best practices for optimizing factory efficiency and productivity with IoT
To make the most of IoT in your factory and maximize efficiency and productivity, consider implementing the following best practices:
- Set clear goals: Define clear goals and objectives for your IoT implementation. This will help you stay focused and measure the success of your efforts accurately.
- Involve employees: Involve your employees in the IoT implementation process. Provide training and ensure that they understand the benefits of IoT. Their support and participation are crucial for the success of the implementation.
- Collect and analyze relevant data: Collect and analyze data that is relevant to your factory’s operations. Focus on key performance indicators (KPIs) that directly impact efficiency and productivity.
- Continuously monitor and optimize: Implement real-time monitoring and analytics to identify areas for improvement. Continuously optimize your processes based on the insights gained from data analysis.
- Embrace predictive maintenance: Leverage IoT to implement predictive maintenance strategies. Monitor the condition of your machines and equipment in real-time, and schedule maintenance activities proactively to prevent breakdowns and maximize uptime.
- Collaborate with suppliers and partners: Extend the benefits of IoT beyond your factory walls by collaborating with suppliers and partners. Share relevant data and insights to optimize the entire supply chain and drive collective efficiency improvements.
By following these best practices, you can unlock the full potential of IoT and transform your factory into a highly efficient and productive operation.
Real-time monitoring and predictive maintenance with IoT
One of the most significant advantages of implementing IoT in your factory is the ability to monitor your equipment in real-time and perform predictive maintenance. Real-time monitoring enables you to track the performance of your machines and identify any anomalies or potential issues as they happen. This allows you to take immediate action and prevent costly breakdowns or production delays.
With IoT-enabled sensors, you can collect data on various parameters such as temperature, vibration, and energy consumption. By analyzing this data, you can identify patterns and trends that indicate the health and performance of your machines. This enables you to predict when maintenance is required and schedule it proactively, minimizing downtime and maximizing productivity.
Predictive maintenance not only saves costs but also extends the lifespan of your equipment. By addressing potential issues before they escalate, you can prevent further damage and ensure that your machines operate at their optimal levels. This also reduces the need for emergency repairs and unplanned maintenance, saving time and resources.
Case studies of successful IoT implementation in factories
Now, let’s take a look at some real-world examples of how IoT has transformed factories and increased efficiency and productivity. One such case study is the implementation of IoT in an automotive manufacturing plant. By connecting their production line equipment and using IoT-enabled sensors, the factory was able to monitor the performance of their machines in real time. This allowed them to identify and resolve issues quickly, resulting in a significant reduction in downtime and an increase in overall productivity.
Another example comes from the food and beverage industry. A large soft drink manufacturer implemented IoT to monitor their production line and ensure the quality of their products. By using sensors to measure temperature, pressure, and other key parameters, they were able to detect deviations from the desired specifications and take immediate corrective actions. This not only improved product quality but also minimized waste and increased customer satisfaction.
These case studies highlight the immense potential of IoT in factory settings. By embracing IoT and leveraging its capabilities, factory owners can achieve remarkable results and gain a competitive edge in the market.
Conclusion
The future of IoT in manufacturing is bright. By embracing IoT and harnessing its capabilities, factory owners can transform their operations and achieve unprecedented levels of efficiency and productivity. From real-time monitoring and predictive maintenance to enhanced inventory management and operational visibility, IoT offers a range of benefits that can drive success in today’s competitive market. So, if you’re looking to make your factory more efficient and productive, it’s time to embrace the power of IoT and unlock its full potential.